Watchmaking industry welcomes a brilliant result with large cost savings
Until now, a Swiss watch company used wire eroded tools made of hardened steel for stamping out the surface structure of watch bezels. Using this method our partner was then only getting a tool life of 20-30 pieces. When they came to us they asked if we could find a solution that would not only give them a more economic result but also will offer a cosmetic appeal as well.
When producing watch components, efficiency is not the only variable to consider. Esthetic appeal is of equal if not greater importance, especially to the consumer. Once working closely with our customer, we developed a punch made of EXTRAMET tungsten carbide where the surface is left with a brilliant polish.
Now our punches have stamped out thousands of watch bezels without any traces of a flawed surface. Once manufacturing started with the new tool our customer was also able to increase the speed of production along with their consistency. Our clients have expressed their satisfaction: “The surface finish is excellent! Until now we never thought it was possible to have these brilliant results.”
In addition to the improved quality, the costs were reduced by 80 percent. These factors have led to the company manufacturing all of their complex tools from tungsten carbide and have selected us as their new solution partner for future applications.
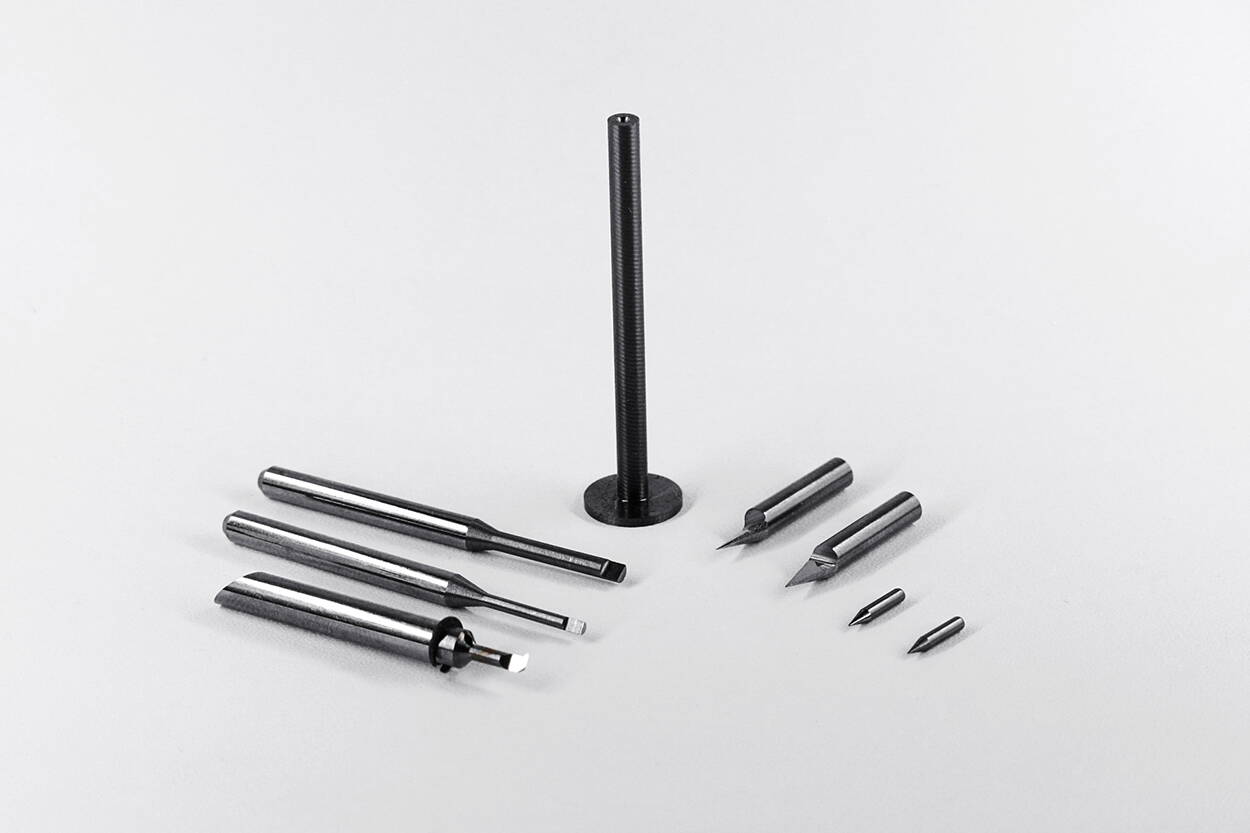
Blanks and parts for the watch industry
Left: Turning tool blank
Center: T-cutter blank
Right: Engraving needle
For further information please contact us.
EXTRAMET AG
Rüttistrasse 42
1716 Plaffeien
Switzerland